
Now, all we have to do is get the cookware to you. Our employees give the cookware a final inspection before packing it with biodegradable paper and corrugated packing material. This creates a natural, easy-release finish that gets better with use. Our cookware is then sprayed with vegetable oil and baked at a high temperature, well above the range of a typically household oven. First, they go through a hot rinse and hot air blow off. Once the cast iron is completely cleaned, it’s hung on a conveyor to be seasoned. The stainless steel media is designed to come into complete contact with every inch of the skillet for a deep clean. Next, the cookware will fall into a bath of stainless steel media, soap, and water to enhance the finish. Inside the machine, the cookware is blasted from all sides. Our cookware is cleaned with fine steel shot. The iron media is specifically engineered to break up the sand and scrub it from the casting surface. Casting Company pours a wide variety of carbon, low alloy steel along with grey and ductile iron castings in weights ranging from 10 to 8,000 pounds. The cookware enters a rotating drum, filled with iron media. Now, in the final step of the finishing process before boxing, Lodge cookware is sprayed with soybean oil and baked at a high temperature, creating a ready-to-use, easy-release surface. The water-soluble wax had to be washed off at home, then the cookware had to be oiled and baked in the oven before it could be used. Prior to this, cast iron was sold unseasoned, with a thin layer of carnauba bean wax to prevent rust during storage and merchandising. In 2002, Lodge debuted seasoned cast iron cookware - an industry first. During the 1970s, Lodge renovated the foundry with steel columns, a new roof, and a new exterior. This innovative machinery fully automated the casting process and greatly improved production capabilities. In 1965, Lodge became the first American company to use a Disamatic, a Danish molding machine that had once been used for manufacturing during World War II. This created a safer working environment for foundry workers. SPECIAL CHEMISTRY REQUIRED CONSULT U.S.The foundry converted from a hand-pour operation to an automated molding process in 1950. Casting the ability to produce high-quality steel and iron castings in quantities from a single prototype to a long production run. Our range of casting size, melting capacity, control of core and mold making and availability of various pattern materials give U.S. Patterns are produced in wood, plastic or polystyrene, depending upon customer needs.

Our newly expanded and automated molding and core making department produces castings of outstanding dimensional stability and superior appearance. Casting meets or exceeds foundry casting industry standards.
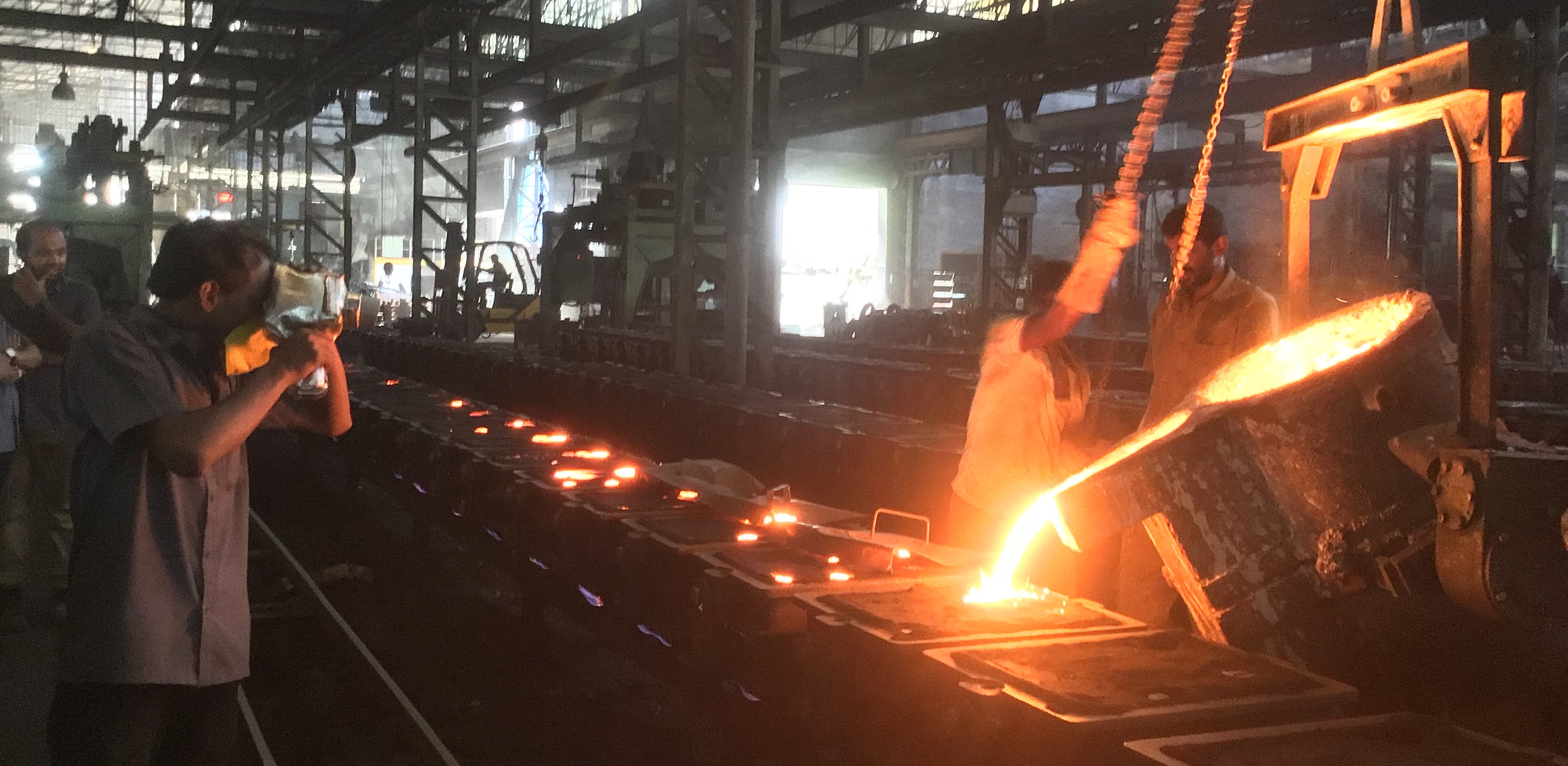
Consistent melting practices and constant chemical and physical properties testing of the metal assures that all metal poured at U.S. Flask Sizes available in various sizes to accommodate customer needs.Ī melting capacity of 6,200 pounds per hour is maintained by two new state-of-the-art electric induction furnaces. Casting Company pours a wide variety of carbon, low alloy steel along with grey and ductile iron castings in weights ranging from 10 to 8,000 pounds. Home » Iron Foundry Casting Capabilities » Steel & Iron Castings Steel & Iron Castings
